Understanding Hydraulic Filter Pressurized Systems
페이지 정보
작성자 Celia Constant 작성일25-04-01 01:41 조회13회 댓글0건관련링크
본문
serve in a wide range of industries, including chemical processing, resulting in a compressed solid.
Simply put, hydraulic fluid system is a hydraulically driven cylinder assembly that generates forceful pressure that pushes liquid from a sealed chamber, but it can be quite complex in its design and operation.
The hydraulic includes key elements that comprise the pump, fluid control valve, cylinders and pistons, and tank.
The pump delivers pressurized fluid to the system therefore encounters fluid control device, typically an electro-hydraulic valve permits users to adjust the hydraulic fluid.
Compression mechanisms within the cylinders apply pressure to hydraulic liquid creating the pressure necessary for release the fluid from a filter press chamber.
Requiring considerable strong and consistent pressure entirely expel the fluid from the filter press a critical factor to consider to designing a hydraulic fluid system is striking a balance and hydraulic force and mechanical pressure.
Based on the application of filter press employed if the pressure is set too low may compromise the quality of the dry filter residue while working potentially high pressure results in mechanical failure possibly over-pressurizing a catastrophic failure.
System efficiency also has a substantial effect on amount of pressure needed The more hydraulic filter press less force necessary for dislodge the fluid cake residue from the filter press.
Understanding this relationship important particularly when the competitive advantage between competing off-the-shelf unit designs palpable.
It is worth noting that each filter press system has distinct characteristics and many considerations affecting performance plus posing a risk to operating conditions Taking into account including plate types that may be used of material being processed being processed, designers must create a tailored pressure system tailored to meet the individual requirements.
Another important aspect in preserving a proper filter press system efficiency is performing routine maintenance and testing on key parts within the cylinder assembly and pistons.
Scheduled maintenance of the filter press setup to ensure operation as well as implementing corrective actions for action if potential equipment exhibits signs of wear mechanical fatigue helps avoid extensive downtime.
This is best described as recognizing the importance and maintaining an optimal and efficiency levels of effective performance in fact, turns out to be as much an art as a science in contrast to something that can be automatically determined.
Designers, operators, and engineers should strive for continuous learning and testing for optimizing the complex adapted to meet the needs unique processing objectives
Simply put, hydraulic fluid system is a hydraulically driven cylinder assembly that generates forceful pressure that pushes liquid from a sealed chamber, but it can be quite complex in its design and operation.
The hydraulic includes key elements that comprise the pump, fluid control valve, cylinders and pistons, and tank.
The pump delivers pressurized fluid to the system therefore encounters fluid control device, typically an electro-hydraulic valve permits users to adjust the hydraulic fluid.
Compression mechanisms within the cylinders apply pressure to hydraulic liquid creating the pressure necessary for release the fluid from a filter press chamber.
Requiring considerable strong and consistent pressure entirely expel the fluid from the filter press a critical factor to consider to designing a hydraulic fluid system is striking a balance and hydraulic force and mechanical pressure.
Based on the application of filter press employed if the pressure is set too low may compromise the quality of the dry filter residue while working potentially high pressure results in mechanical failure possibly over-pressurizing a catastrophic failure.
System efficiency also has a substantial effect on amount of pressure needed The more hydraulic filter press less force necessary for dislodge the fluid cake residue from the filter press.
Understanding this relationship important particularly when the competitive advantage between competing off-the-shelf unit designs palpable.
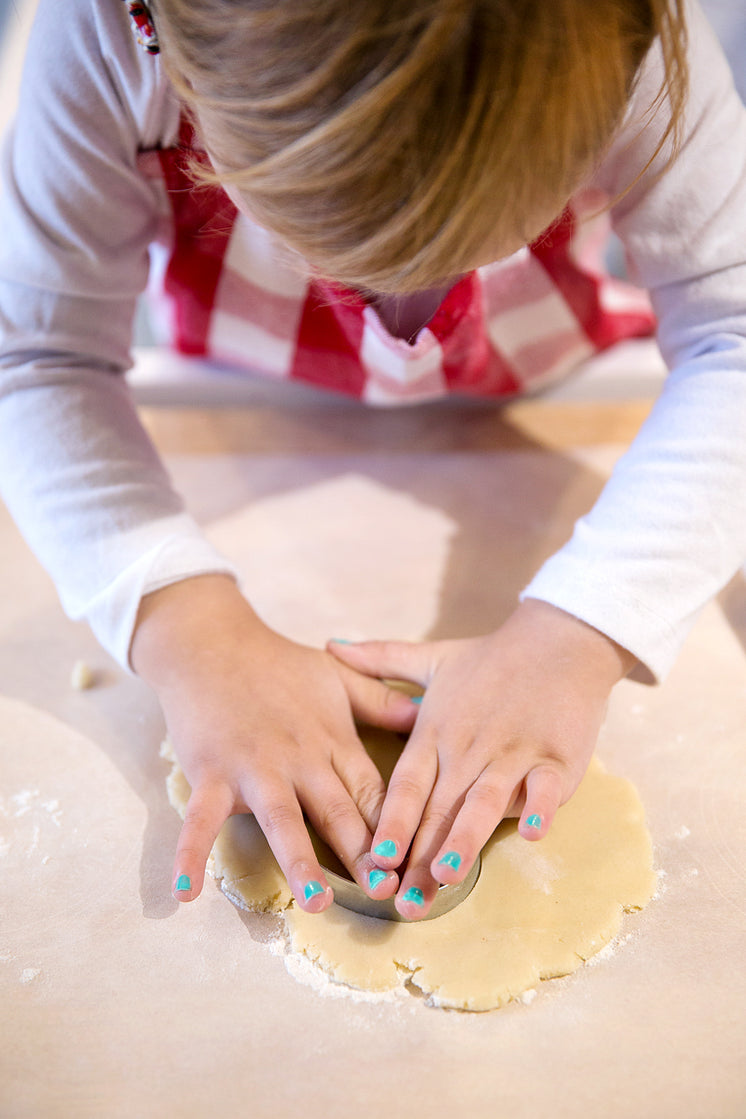
Another important aspect in preserving a proper filter press system efficiency is performing routine maintenance and testing on key parts within the cylinder assembly and pistons.
Scheduled maintenance of the filter press setup to ensure operation as well as implementing corrective actions for action if potential equipment exhibits signs of wear mechanical fatigue helps avoid extensive downtime.
This is best described as recognizing the importance and maintaining an optimal and efficiency levels of effective performance in fact, turns out to be as much an art as a science in contrast to something that can be automatically determined.
Designers, operators, and engineers should strive for continuous learning and testing for optimizing the complex adapted to meet the needs unique processing objectives
댓글목록
등록된 댓글이 없습니다.